When it comes to crafting smooth curves in concrete structures, plywood curved concrete forms make a significant difference. These versatile forms help achieve the desired curvature while ensuring the integrity of the concrete during the pouring and setting processes. This article dives into understanding these forms, the techniques for their effective use, and maintaining them for long-lasting results.
Understanding Plywood Curved Concrete Forms
Plywood curved concrete forms are essential tools for creating aesthetically pleasing and structurally sound concrete installations. By using plywood, which is lightweight yet durable, contractors and DIY enthusiasts can fabricate custom shapes that are both functional and visually appealing.
In conclusion, the art of creating smooth curves with plywood curved concrete forms lies in understanding the materials involved, mastering the techniques, and maintaining the tools. By following the outlined steps and troubleshooting effectively, you can achieve beautiful concrete structures that stand the test of time.
The Basics of Plywood and Concrete
Plywood is a manufactured wood panel made from thin sheets of wood veneer, glued together. Its flexibility allows it to bend into curves, making it an ideal material for forming shapes in concrete applications. Concrete, on the other hand, is a composite material composed of fine and coarse aggregates bonded together with a fluid cement paste.
Understanding the properties of both materials is crucial. Plywood provides a supportive structure while concrete adds weight and permanence. As concrete is poured into these forms, it undergoes a chemical reaction known as hydration, which solidifies it and forms a sturdy structure. The interaction between the plywood and the concrete is also significant; the smooth surface of the plywood helps in achieving a fine finish on the concrete, minimizing the need for extensive post-pour surface treatments.
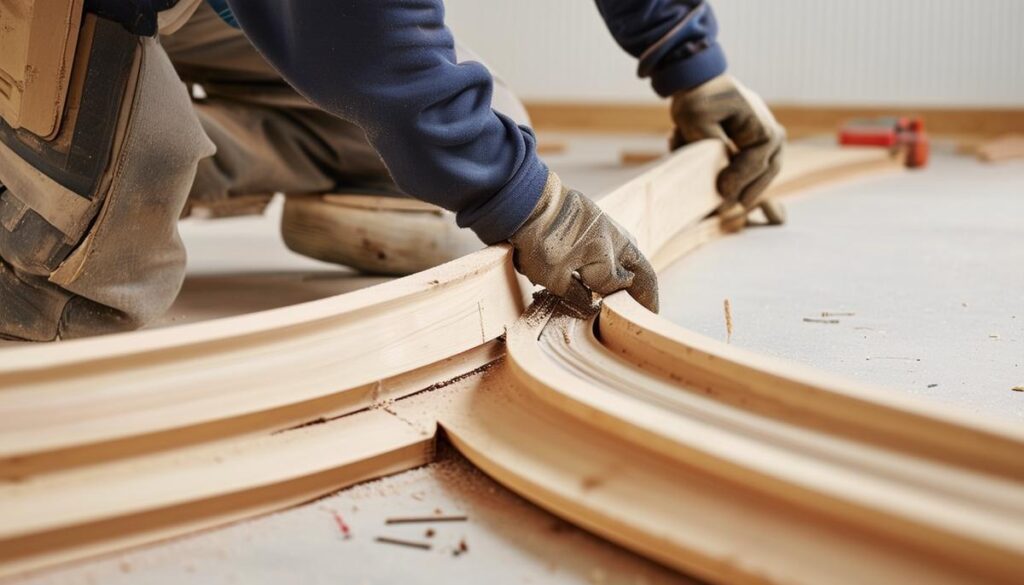
The Role of Forms in Concrete Work
Forms serve a fundamental purpose in concrete work. They hold the concrete in place until it sets, ensuring that the desired shape is maintained. Without proper forms, concrete would not be able to achieve the intricate designs necessary for modern construction.
When using plywood for curved forms, builders can create everything from gentle arcs to complex shapes. Plywood forms can be customized to any project, allowing for artistic expression in buildings, bridges, and landscape architecture. The versatility of plywood also means that it can be easily cut and shaped on-site, enabling quick adjustments to be made as designs evolve. Furthermore, the use of plywood forms can significantly reduce labor costs and time, as they are often reusable for multiple projects, making them a sustainable choice in the construction industry.
In addition to their practical applications, plywood curved concrete forms can also enhance the overall aesthetic of a project. Designers can leverage the natural grain and texture of plywood to create unique visual elements that complement the concrete’s finish. This synergy between materials not only serves a functional purpose but also contributes to the artistic narrative of the structure, allowing for a seamless blend of form and function. As architects and builders continue to explore innovative design possibilities, the role of plywood forms in shaping the future of concrete construction remains pivotal.
The Art of Creating Smooth Curves
Creating smooth curves takes both skill and knowledge of best practices. By focusing on precision and employing effective techniques, anyone can achieve beautiful, curved concrete features.
Importance of Precision in Curve Creation
Precision is the cornerstone of successful curve creation. Any deviation from the desired shape—whether in the curve of the plywood or the angle of the formwork—can lead to flaws in the final concrete product. Consistency in measurements, alignment, and spacing is vital.
Furthermore, attention to detail during the setup phase will pay dividends when it comes to achieving smooth curves. Before pouring, double-check all dimensions and ensure that the form is adequately supported to prevent sagging or misalignment. This meticulous approach not only enhances the aesthetic appeal of the concrete but also contributes to its structural integrity, ensuring that the curves are not just visually pleasing but also durable over time.
Techniques for Achieving Smoothness
To achieve a smooth finish in curved concrete, consider the following techniques:
- Use High-Quality Materials: Select plywood that is free from knots and imperfections that could disrupt the concrete surface.
- Moisture Control: Apply a release agent to the inner surface of the forms. This helps in preventing the concrete from sticking and guarantees a smoother finish when the forms are removed.
- Palm Smoothing: After pouring, use a palm tool to gently smooth the surface of the wet concrete to eliminate any minor imperfections.
By incorporating these techniques, the risk of common problems can be minimized, leading to a more refined final product. Additionally, experimenting with different tools and methods can yield even better results; for instance, using a concrete edger can help create a more defined edge along the curves, enhancing the overall design. It’s also beneficial to consider the temperature and humidity levels during the curing process, as these environmental factors can significantly affect the finish and strength of the concrete.
Moreover, the choice of concrete mix can play a crucial role in achieving smooth curves. A mix with a finer aggregate can lead to a smoother surface, while additives such as plasticizers can improve workability, allowing for better manipulation of the concrete during the pouring phase. Understanding the properties of the materials at your disposal will empower you to make informed decisions that elevate the quality of your curved concrete projects. Read more about pouring at https://artschoolptbo.org/course/acrylic-pour-workshop-cloud-pour/
Step-by-Step Guide to Using Plywood Curved Concrete Forms
Using plywood curved concrete forms entails a systematic approach that can be broken down into manageable steps. The following guide will help both beginners and seasoned pros execute the process effectively.
Preparing Your Plywood
The first step involves selecting and preparing the plywood. Choose a thickness appropriate for the curve and load. Typically, ½ inch to ¾ inch thick plywood works well for many applications. Cut the plywood into the desired shape using a jigsaw or circular saw, ensuring all cuts are smooth and even.
After cutting, treat the edges with sandpaper to prevent splinters and promote a smoother surface contact with the concrete. Applying a waterproof sealant is also recommended to help maintain the integrity of the wood while allowing for easy removal later on. Additionally, consider using a primer before sealing, as this can further enhance the plywood’s durability and resistance to moisture, which is particularly important in outdoor projects.
Setting Up Your Concrete Forms
Once the plywood is prepared, it’s essential to set up the forms correctly. Begin by securing the curved forms in place using stakes driven into the ground or additional supports that hold the forms firm against the earth’s surface. Ensure that the top edges of the forms align perfectly at the desired height.
Check for plumb and level at multiple points along the structure to avoid any discrepancies. It may be beneficial to use a level for larger curves to ensure that each section conforms to the intended shape throughout the entire form. Additionally, consider using a string line for longer curves to maintain a consistent radius, which can be particularly helpful in achieving a professional-looking finish. This extra step can save time and reduce the need for adjustments later on.
Pouring and Shaping the Concrete
With the forms in position, it’s time to mix and pour the concrete. Follow the manufacturer’s instructions for mixing the ingredients, ensuring you achieve the correct consistency to minimize air bubbles and achieve a solid pour.
As you pour, work in increments, allowing the concrete to settle into the forms. Use a bull float or similar tool to spread the concrete and ensure that it coats the entire interior of the form. This methodically helps in eliminating air pockets that might lead to imperfections. After the initial pour, consider using a vibrating tool to further consolidate the concrete, especially in tighter curves where air may be trapped. This technique not only enhances the density of the concrete but also improves the overall finish, resulting in a more robust and aesthetically pleasing final product.
Read more about plywood formwork at: Plywood Formwork The Ultimate Guide for Builders
Troubleshooting Common Issues
Even when following best practices, issues can arise during the process. Being aware of common problems enables you to address them swiftly and maintain the quality of your project.
Dealing with Plywood Warping
One challenge that may occur is warping of the plywood forms. Plywood is susceptible to fluctuations in moisture and temperature. If the wood begins to warp, it can lead to misalignment in the curves.
To combat warping, always store plywood in a dry, flat environment. If warping occurs despite precautionary measures, it may be necessary to clamp the plywood back into shape or replace sections as needed before pouring concrete. Additionally, consider using marine-grade plywood, which is treated to resist moisture and is less prone to warping, especially in humid climates. Regularly inspecting the plywood for signs of stress or bending during the project can also help catch issues early, allowing for timely adjustments. To learn more about marine click here.
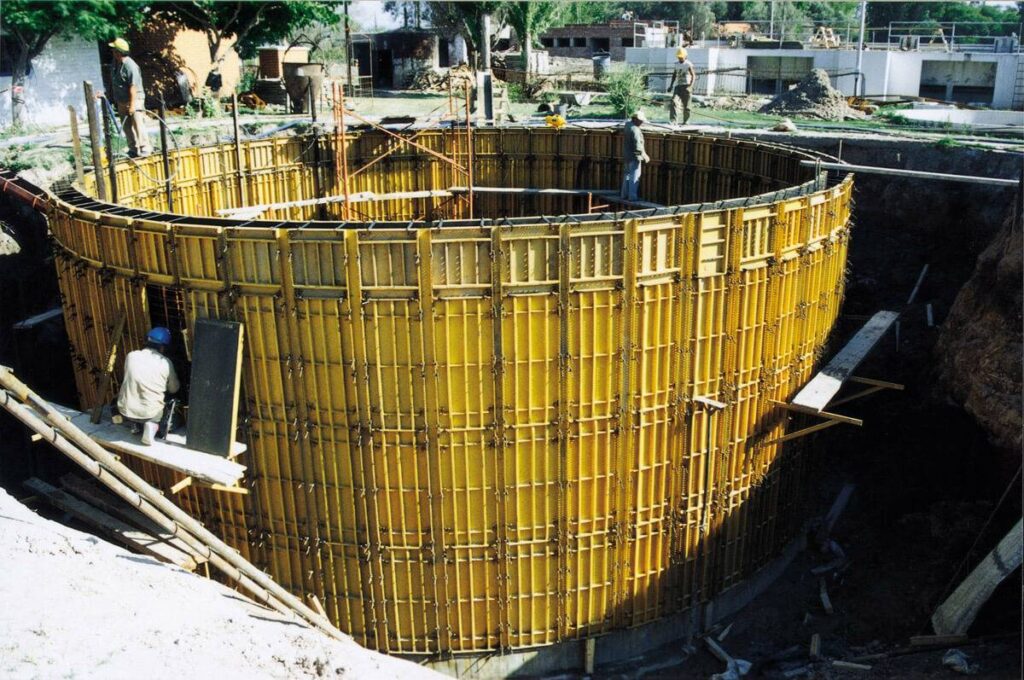
Addressing Concrete Cracks and Bubbles
After the concrete sets, you might discover cracks or bubbles on the surface. Cracks can indicate that the mix was too dry or that the curing process was rushed. Bubbles generally form due to trapped air and inadequate settling.
To address these issues, allow the concrete to cure for a sufficient time. If cracks are significant, consider using a concrete repair compound appropriate for the project. For bubbles, a trowel may smooth the surface if caught early enough. It’s also beneficial to implement proper vibration techniques during the pouring process to minimize air pockets. Using a concrete vibrator can help ensure that the mix settles evenly, reducing the likelihood of bubbles forming. Furthermore, maintaining a consistent moisture level during the curing phase is crucial; covering the concrete with wet burlap or plastic sheeting can help retain moisture and promote even curing, ultimately leading to a stronger, more resilient surface.
Maintaining Your Plywood Curved Concrete Forms
Proper maintenance of your plywood curved concrete forms ensures longevity and continual effectiveness for future projects. Neglect can lead to premature wear, making them less effective over time.
Cleaning and Storing Your Forms
After each use, clean the forms thoroughly. Remove any excess concrete promptly, as dried concrete can damage the surfaces and make removal more difficult in the future. A stiff brush or pressure washer can be effective in scraping away buildup without damaging the plywood.
When storing forms, keep them in a dry, protected environment. Stack forms in a manner that prevents warping, and use spacers between sheets to allow airflow and avoid moisture accumulation.
When to Replace Your Forms
Even with diligent care, there may come a time when replacement is necessary. Signs that your plywood forms are due for replacement include severe warping, cracks, or significant wear and tear. It’s essential to avoid using forms in poor condition for your future projects, as they may compromise the quality of the concrete work.
Investing in new forms periodically will ensure you always have reliable equipment to produce smooth, beautiful curves in your concrete projects.