Plywood Formwork: The Ultimate Guide for Builders
Plywood formwork is an essential process in the construction industry, providing a strong and flexible solution for creating concrete structures. This guide aims to inform builders on the various aspects of plywood formwork, its types, selection criteria, usage, and maintenance.
Understanding Plywood Formwork
Definition and Basic Concept of Plywood Formwork
Plywood formwork refers to the temporary structures made from plywood that are used to mold concrete into desired shapes during construction. This method is highly effective for creating walls, slabs, columns, and other elements. The purpose of the formwork is to hold the liquid concrete in place until it cures and sets, maintaining its shape and providing support.
Due to its lightweight nature, plywood formwork allows for easy handling and transportation on construction sites. The versatility of plywood enables it to be customized to meet the specific requirements of various projects. Additionally, the surface finish of plywood can be modified to achieve different textures and appearances in the final concrete product, which can be particularly beneficial for architectural applications where aesthetics are important.
Importance of Plywood Formwork in Construction
Plywood formwork plays a crucial role in modern construction techniques. Here are some key reasons why it is vital:
- Cost-effectiveness: Plywood is relatively inexpensive compared to other formwork materials, making it a popular choice among builders.
- Speed of construction: Due to its lightweight and ease of assembly, plywood formwork significantly speeds up the construction process.
- Reusable: High-quality plywood can be reused multiple times, which adds to its cost efficiency.
- Customizable: Builders can easily cut and shape plywood to fit the unique specifications of their projects.
- Durability: Plywood is strong enough to withstand the pressures of wet concrete, ensuring that the molded structures maintain their integrity.
Moreover, plywood formwork is not only advantageous in terms of functionality but also contributes to sustainability in construction. The ability to reuse plywood reduces waste and minimizes the demand for new materials, aligning with eco-friendly building practices. Additionally, advancements in plywood treatment and sealing technologies have improved its resistance to moisture and wear, further extending its lifespan and usability on various projects. As the construction industry continues to evolve, the integration of plywood formwork remains a testament to the balance between efficiency, cost, and environmental responsibility.
Furthermore, the adaptability of plywood formwork extends beyond just shapes and sizes; it can also be used in conjunction with other materials to enhance performance. For instance, combining plywood with steel reinforcements can provide additional strength for larger structures, while still maintaining the lightweight benefits of plywood. This hybrid approach allows for innovative construction solutions that meet the rigorous demands of modern engineering while keeping costs manageable. As builders and architects explore new designs and structural possibilities, plywood formwork will undoubtedly remain a key player in shaping the future of construction.
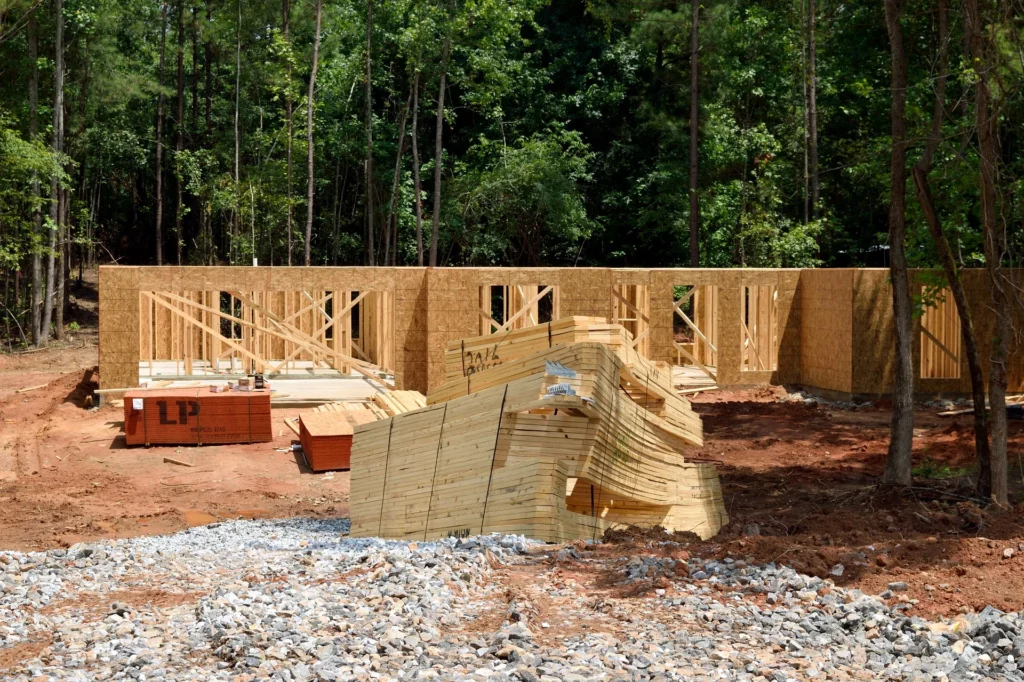
Types of Plywood for Formwork
Marine Plywood
Marine plywood is specifically designed to resist moisture and decay, making it suitable for formwork applications in environments where water exposure is a concern. It is constructed with high-quality veneers that are bonded together using waterproof adhesives. This type of plywood provides a smooth surface finish and is ideal for casting concrete in wet conditions or areas prone to high humidity. Find more about humidity at https://energyresearch.ucf.edu/consumer/buildings/building-science-basics/humidity/
Builders appreciate marine plywood for its robustness and longevity, which can significantly reduce the costs associated with frequent replacements. Furthermore, the use of marine plywood can enhance the overall durability of the construction, as it is less likely to warp or swell when exposed to moisture. This characteristic is particularly important in coastal areas or regions with high rainfall, where traditional plywood may fail to perform adequately over time. Additionally, marine plywood is often treated with preservatives that further protect it from fungal and insect damage, ensuring that the structural integrity of the formwork remains intact throughout the construction process.
Shuttering Plywood
Shuttering plywood is another popular type used in formwork applications. It is fabricated for use specifically in construction forming. Shuttering plywood comes with a film overlay, which not only enhances its durability but also provides a smooth surface finish that helps minimize imperfections in the concrete.
This type of plywood is perfect for projects requiring precise finishing or complex forms due to its resistance to warping and moisture absorption. Builders often choose shuttering plywood for its balance of cost and performance. The film overlay also makes it easier to clean and reuse, which can be a significant advantage on large projects where time and resources are limited. Moreover, shuttering plywood is available in various thicknesses and sizes, allowing builders to select the most suitable option for their specific project requirements. Its versatility extends beyond just concrete formwork; it can also be utilized in creating temporary structures, such as scaffolding and staging, making it a valuable asset in the construction toolkit.
BWP (Boiling Water Proof) Plywood
BWP plywood is an advanced type of plywood that features extraordinary water-resistant characteristics, making it ideal for formwork exposed to harsh environmental conditions or moisture. It is manufactured using special adhesives that withstand boiling water, ensuring the plywood does not delaminate or deform under stress.
This plywood type is particularly beneficial in regions with heavy rainfall or for structures that are located near water bodies, as it can maintain its structural integrity under extreme moisture conditions. Additionally, BWP plywood is often used in applications where prolonged exposure to water is unavoidable, such as in the construction of bridges, docks, and other infrastructure projects. Its resilience not only contributes to the longevity of the formwork but also enhances the quality of the finished concrete by preventing water-related defects. Furthermore, BWP plywood can be treated with fire retardants, adding an extra layer of safety in construction environments where fire hazards are a concern, making it a versatile choice for builders looking to meet various project specifications while ensuring durability and safety.
Selecting the Right Plywood for Formwork
Factors to Consider
Choosing the right plywood for formwork is critical to the overall success of a construction project. Several factors should be first taken into consideration:
- Durability: Assess the durability requirements based on the environmental conditions the formwork will face.
- Cost: Evaluate your budget and find a suitable plywood type that meets both quality and cost criteria.
- Ease of handling: Choose lightweight options for easy transportation and installation.
- Surface finish: Consider the surface finish needed for the final concrete product; smoother surfaces reduce finishing work later.
In addition to these key factors, it’s also important to think about the longevity of the plywood. Some projects may require formwork that can be reused multiple times, which would necessitate selecting a higher-grade plywood that can withstand repeated use without significant wear. Furthermore, the type of concrete mix being used can influence your choice; for instance, more aggressive mixes may require a more robust formwork solution to prevent damage during the curing process. Always consult with your project manager or a construction specialist to ensure you are making the most informed decision possible. Click here to find more about damage.
Plywood Grades and Their Significance
Plywood is graded based on its quality and characteristics. Understanding these grades is essential for selecting the right product:
- Grade A: This top quality plywood has a smooth surface with minimal imperfections and is ideal for projects requiring a high-quality finish.
- Grade B: Plywood in this grade may have a few visible knots but still maintains a smooth surface, suitable for many construction applications.
- Grade C: This grade contains more knotholes and repairs but is still structurally sound, often used for less visible areas of formwork.
- Grade D: Plywood with numerous imperfections, primarily utilized where appearance is not a critical concern.
When selecting plywood grades, it’s also beneficial to consider the specific requirements of your project. For example, if the formwork is to be exposed to moisture, opting for exterior-grade plywood, which is treated for water resistance, can prevent warping and degradation over time. Additionally, understanding the local regulations and standards for construction materials can guide you in making compliant choices that ensure safety and performance. Each grade serves a unique purpose, and knowing when to utilize each type can save both time and resources in the long run.
Steps in Using Plywood Formwork
Designing the Formwork
The first step in using plywood formwork is designing it according to the requirements of the concrete structure. A well-thought-out design should account for factors such as dimensions, load-bearing requirements, and any architectural features that need to be incorporated.
Utilizing software for structural design can help builders create detailed plans, ensuring that each component is appropriately calculated to handle the pressures exerted by the wet concrete.
Assembling the Formwork
Once the design is complete, the next step is assembling the plywood formwork. Start by cutting the plywood sheets according to the specified dimensions. Ensure that all edges are cleanly cut to facilitate smooth joining.
Add support beams and braces to reinforce the structure, especially if dealing with larger forms. The assembly process should be done carefully to avoid gaps or misalignments that could affect the final finish of the concrete.
Pouring Concrete into the Formwork
After the formwork is secured and verified for stability, it’s time to pour the concrete. Proper pouring techniques are vital to ensure that the concrete fills all areas of the formwork. Use a concrete vibrator to eliminate air pockets and ensure proper consolidation.
Once the concrete is poured, smoothly finish the surface where necessary, keeping in mind that the smoother the pour, the reduced amount of finishing work needed later. Allow adequate time for the concrete to cure before removing the formwork.
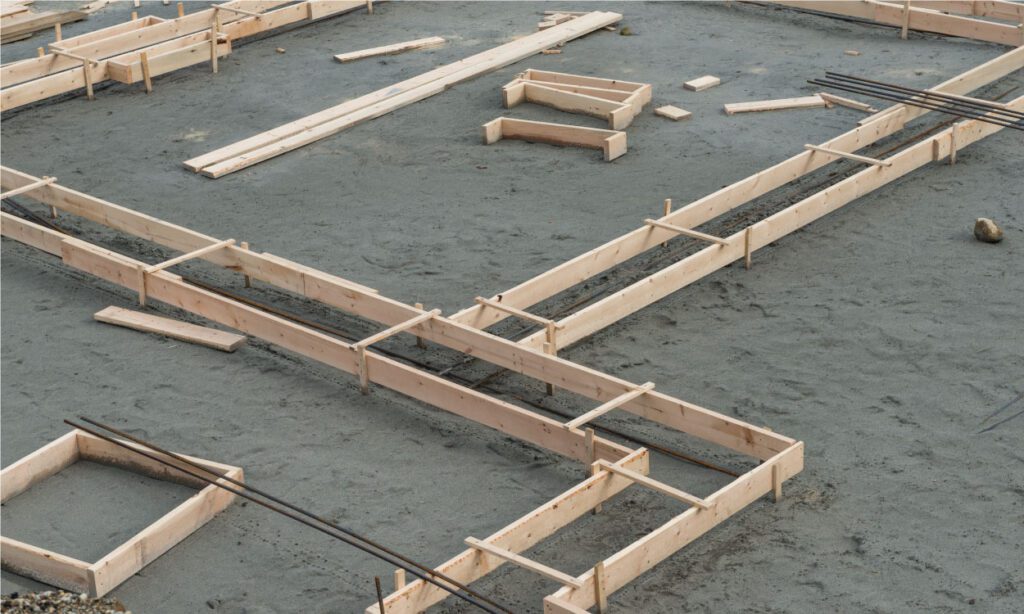
Maintenance and Care of Plywood Formwork
Cleaning and Storing Plywood Formwork
To extend the life of plywood formwork, regular cleaning is essential. After each use, clean the formwork to remove any concrete residue, dirt, or debris. A damp cloth or sponge is typically sufficient, but stubborn stains may require a mild cleaning solution.
Once cleaned, store the plywood in a dry, sheltered location, preferably stacked flat to prevent warping or bending. Avoid placing heavy materials on top of them, and cover them to protect against moisture.
Extending the Lifespan of Your Plywood Formwork
To maximize the lifespan and functionality of your plywood formwork, consider implementing the following strategies:
- Use release agents: Applying a release agent before pouring concrete can help minimize adhesion and protect the plywood surface.
- Inspect regularly: Conduct regular inspections for any signs of damage or wear, and replace any compromised sheets promptly.
- Avoid excessive moisture: Keep plywood protected from rain and excess moisture to prevent quality degradation.
- Store properly: Follow best practices for storing formwork to avoid deformation or damage when not in use.
By following these guidelines, builders can ensure that their plywood formwork remains effective, enhancing the quality of their concrete structures and optimizing construction efficiency.
Learn about curved form plywood at: Creating Smooth Curves with Plywood Curved Concrete Forms